金属和合金化学镀前的处理方法与过程与电镀前的处理工艺大致相同,具体工艺方法可以参考第三章和第四章的相关内容。另外,不同材料的前处理工艺有所不同,在选择前处理工艺流程时,要了解材料的种类和表面状况。
1.碳钢和低合金钢的前处理
在化学镀加工对象中,以碳钢和低合金钢工件最为普遍,虽然有各种不同的镀前处理方法可供选择,但是参考规范化的工艺总是有益的,典型的碳钢和低合金钢工件的前处理工序如下,有关前处理溶液的组成和使用方法见表7-1。
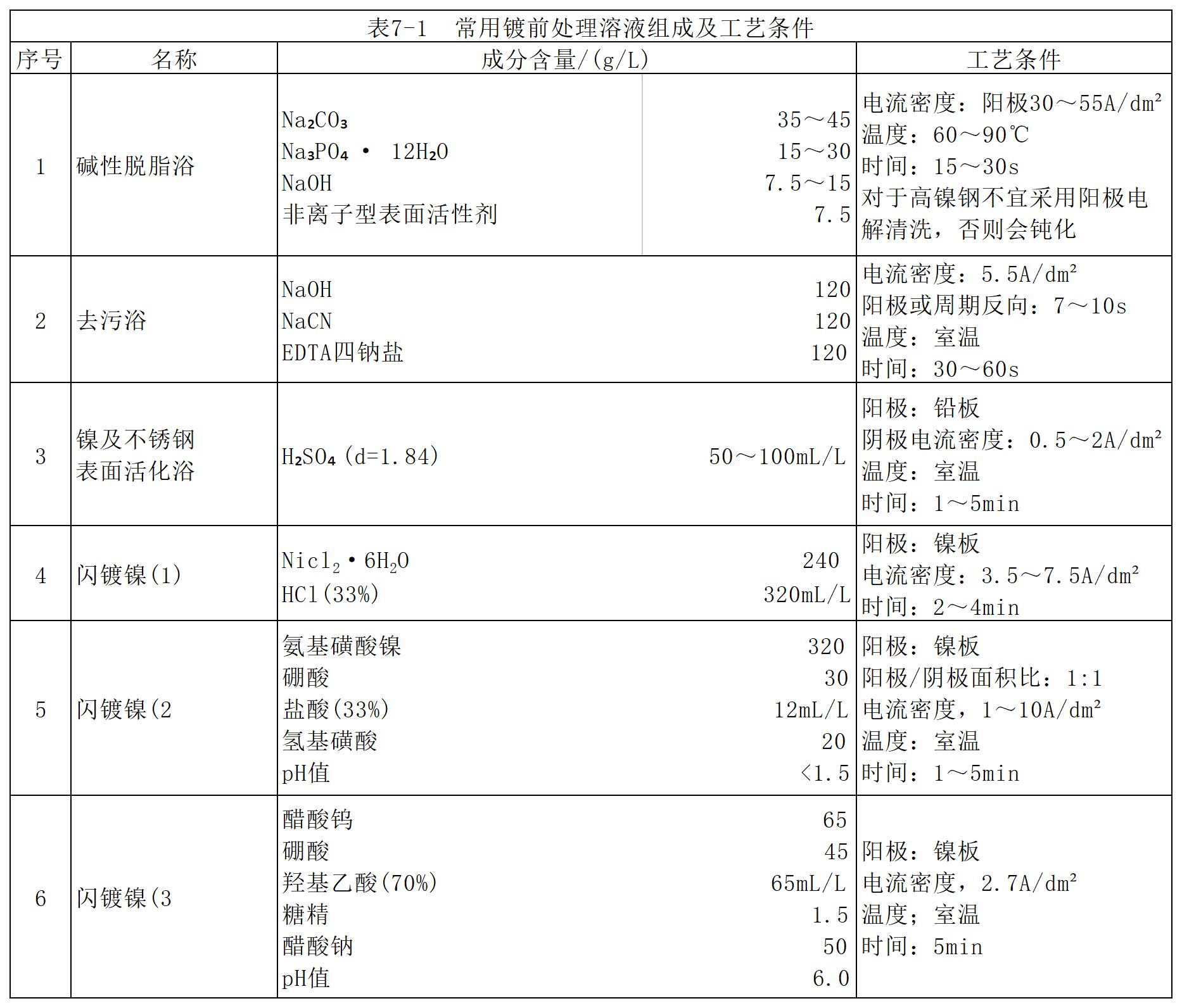
(1)化学除油 含表面活性剂的碱性脱脂浴,70~80℃,10~20min。
(2)热水清洗70~80℃,2min。
(3)冷水清洗 两次逆流漂洗或喷淋,室温,2min。
(4)电解清洗 碱性脱脂浴,60~80℃,15~30s,阳极3~10A/dm²。
(5)热水清洗70~80℃,2min。
(6)冷水清洗 两次逆流漂洗或喷淋,室温,2min
(7)浸酸活化 室温,0.5~1min
(8)冷水清洗 两次逆流漂洗或喷淋,室温,1min。
(9)去离子水洗或预热浸洗 70~80℃,3min
对于有锈蚀或氧化皮的工件,应在初步除油之后,采用酸洗、喷砂或钢丝刷子除净锈蚀和氧化皮。钢铁件酸洗时间不宜过长,酸洗除锈液中要加入缓蚀剂,以避免过腐蚀。若采用盐酸酸洗后,工件表面出现不易除净的黑色污泥状物时,则可以采用表7-1中方法2进行除污处理。当工件基体含碳量大于0.35%,或者合金成分含量较高时,可考虑在镀前采取表7-1闪镀镍(1)的工艺,预先在工件上电镀一薄层镍,这种方法有利于保证化学镀镍与工件基体的结合强度。
2.铸铁件的镀前处理
铸铁有许多种类,常见的铸铁件为灰铸铁,含碳量为2%4%,主要以石墨相存在。铸铁件表面疏松多孔,特别是当铸造质量不高的情况下,铸铁件表面缺陷尤为突出,因此,铸铁化学镀镍比较困难,废品率较高。主要表现在镀层结合强度差,镀层孔隙率高,镀件容易返锈。因此铸铁件的镀前处理应十分仔细。灰铸铁的典型前处理工艺如下。
(1)化学除油 含清洁剂的碱性脱脂溶液(见表7-1),70~80℃,时间10~20min。
(2)热水清洗 70~80℃,2min。
(3)冷水清洗 两次逆流漂洗或喷淋,室温,2min
(4)电解清洗 含表面活性剂的碱性脱脂溶液(见表7-1),70~80℃,工件阳极,电流密度3~5A/dm²,时间2min。
(5)热水清洗 70~80℃,2min
(6)冷水清洗 两次逆流漂洗或喷淋,室温,2min。
(7)浸酸活化 稀硫酸10%(体积分数),室温,15~30s
(8)冷水清洗 两次逆流漂洗或喷淋,室温,1~2s。
(9)重复步骤(4)~(8)步重复操作。
(10)去离子水洗或预热浸洗70~80℃,2min。
(11)化学镀镍 按镀浴工艺参数操作。
(12)冷水清洗两次逆流漂洗或喷淋,2min。
(13)干燥。
对于铸造质量较好的铸件,步骤(9)可省略。铸件酸洗时间不宜过长,否则易造成工件表面碳富集,在镀层与基体之间形成夹心层,降低镀层结合强度。也有参考文献报道,在氧化性的酸中,大电流阳极电解活化铸铁的前处理工艺,工序简述如下。
①脱脂清洗。
②电解活化。硫酸60%(体积分数),室温,工件阳极,电流密度10~20A/dm²,时间30s。
③清洗。
④化学镀镍。
3.不锈钢、高合金钢的镀前处理
由于不锈钢和高镍、铬含量合金钢的表面上有一层钝化膜,若按常规钢铁件表面预处理的方式进行前处理,化学镀层的结合强度很差。在不锈钢、高合金钢件碱性除油之后,可采用表7-1中方法3进行阴极活化处理,以改善镀层的结合强度。为可靠起见,在阴极活化后应采用表7-1中方法4,进行预镀镍处理。典型的镀前处理工艺如下。
(1)化学除油 碱性脱脂浴,参见表7-1中方法1。
(2)热水清洗 70~80℃,2min。
(3)冷水清洗 两次逆漂洗或喷淋,室温,2min
(4)电解清洗 碱性脱脂浴,参见表7-1中方法1,但工件为阴极。
(5)重复步骤(2)~(3)步重复操作。
(6)预镀镍 闪镀浴,参见表7-1中方法4。
(7)冷水清淋 两次逆流漂洗或喷淋,室温,1min。
(8)去离子水洗或预热浸洗 70~80℃,2min
(9)化学镀镍 按镀浴工艺参数操作。
(10)冷水清洗 两次逆流漂洗或喷淋,2min
(11)于燥。
4.铜及铜合金的镀前处理
在次磷酸钠为还原剂的化学镀浴中,铜属于非催化性金属。因此,铜及铜合金工件与钢铁件前处理的主要不同之处在于活化工序。铜件化学镀前的活化方法有多种。
①用已经活化的具有催化活性的金属(如铁丝),接触进入镀浴中的工件。
②铜工件带电入镀浴,阳极为镍板,铜工件为阴极,槽电压1~2V,时间30~60s。
③铜工件预浸氯化钯溶液(Pd:0.01~0.1g/L),催化活化。④预镀镍活化,参见表7-1中方法4。
对于纯铜和黄铜工件,特别是小型工件,镀前活化方法①是简单有效的。然而对含有催化毒性元素的铜合金(如铅黄铜等)则建议使用其他活化方法。对于形状复杂的工件,采用活化方法③比较合理;但是浸钯之后,镀前应彻底清洗,要防止将钯离子带入化学镀浴。预镀镍活化法可十分有效地防止黄铜中有害金属离子溶出而污染化学镀浴;而且对于保证镀层结合强度是有利的;但是由于电镀受电场分布的影响,分散能力差;对于形状复杂的工件,如深孔、盲孔的内表面难以获得预镀镍层。铜及铜合金典型的前处理工序如下。
①化学除油 碱性化学脱脂浴(氢氧化钠的用量要少或者不加),70~80℃,10~20min。
②热水清洗70~80℃,2min。
③冷水清洗 两次逆流漂洗或喷淋,室温,2min
④电解清洗 碱性化学脱脂浴,50~60℃,阴极,5A/dm²,2min。
⑤重复步骤(2)~(3)步重复操作。
⑥预镀镍活化 闪镀浴,见表7-1中方法4。
⑦冷水清洗 两次逆流漂洗或喷淋,室温,2min
⑧去离子水洗或预热浸洗。
⑨化学镀镍 按镀浴工艺参数操作。
⑩冷水清洗 两次逆流漂洗或喷淋,室温,2min。
5.铝及铝合金的镀前处理
铝及铝合金的密度小,导热导电性能较好,是一种高比强度的材料。然而,铝及铝合金本身却存在易腐蚀、不耐磨、接触电阻大、焊接难等缺点。由于采用阳极氧化、涂装、电镀等表面保护技术,促进了铝和铝合金的广泛应用。化学镀镍作为铝和铝合金理想的表面改性技术之一,其重要性正在不断增加。铝是一种难镀的金属基体;由于铝与氧有很强的亲和力,铝基体表面极易生成氧化膜,这种自然氧化膜与其表面覆盖层的结合强度很差。为克服这个问题,至今已经研究开发了数目难以统计的工艺方法,归纳起来有以下三种技术途径。
在通常的脱脂清洗、刻蚀活化工序之后进行。
(1)通过专门的浸镀溶液处理 利用浸镀浴的腐蚀性,除去铝的氧化膜;在受控置换反应下,在铝件表面浸镀上一层尽可能薄的、比较不容易氧化的中间金属层;浸镀层是暂时性的或过渡性的,如浸锌法、浸镍法;然后转入预镀层工序,如预电镀镍或预化学镀镍。
(2)在铝合金表面形成特殊结构的人为氧化膜可防止铝的氧化,提高后续镀层的结合强度,如磷酸阳极氧化法。
(3)直接化学镀镍 如某些弱碱性化学镀浴法等。
至今为止,研究开发和已经生产验证的工艺方法相对集中于采用浸锌-预镀层方法。典型的铝及铝合金前处理工序如下所述,有关前处理溶液的配方组成和工艺条件列于表7-2中。
①化学除油。少或无腐蚀性的脱脂浴,见表7-2中方法1。
②冷水清洗。两次逆流漂洗或喷淋,室温,2min。
③酸洗。见表7-2中方法2。
④重复步骤②。
⑤浸锌(第一次)。见表7-2中方法3。
⑥冷水清洗。

⑦退锌。见表7-2中方法2。
⑧冷水清洗。
⑨浸锌(第二次)。见表7-2中方法3,但时间较短。
⑩冷水清洗。
⑪预镀镍活化。见表7-2中方法5或方法6。
⑫冷水清洗。
⑬去离子水洗或预热浸洗。70~80℃,1min。
⑭化学镀镍。按化学镀镍浴工艺参数操作。由于铝和铝合金工件的加工成型方法以及化学成分不同,其前处理工艺方法应该相应变化。比如对于高硅含量的铸铝合金建议将上述典型前处理工序,步骤③的酸洗浴改用硝酸与氢氟酸的混合酸(3:1体积比)。为提高浸锌法对于各种铝合金的适用性,人们进行多年持续的研究开发,并有多种被称为合金化浸锌的商品浴已经由工业生产证实:这些商品浴对于宽广的铝合金成分范围适用性好,镀层结合强度和成品率较高。据参考文献报道:这种合金化浸锌膜很薄,约0.5μm;其主要化学成分除锌之外,还含12%~30%的铜、镍和铁合金元素;这种商品浸锌浴的缺点在于含有氰化物,因此在操作时应十分小心。出于环境和生态保护的目的,无氰、无氟、无硝酸盐合金化浸锌工艺是研究开发的方向。
6.镁及镁合金的镀前处理
镁合金具有密度小、比强度高以及良好的电磁屏蔽、降噪减震等优异的综合性能,在航空航天、汽车、电子、通信等行业得到了愈来愈广泛的应用。尤其是近十几年来,随着汽车和电子、通信工业的迅猛发展,大量的镁合金零部件被用来代替塑料、铝合金,甚至钢铁零件,成为继钢铁、铝合金之后的第三大金属工程材料。
然而,镁是一种化学性质活泼的元素,镁合金在各种环境介质中的耐腐蚀性能都比较差。为了提高镁合金材料的耐腐蚀性能,通常要对镁合金材料的表面进行处理,在其表面形成具有一定防腐蚀能力的覆盖层。化学镀是镁及镁合金材料可以采用的一种表面防腐蚀处理方法。由于镁的活泼特性,在镁及镁合金镀件表面通常有一层自然的氧化膜,因此,在化学镀之前必须采用特殊的镀前处理方法,去除这层氧化膜和其他污物,以保证镀层和基体的附着力,提高电镀质量。典型的镁和镁合金镀前处理工艺简述如下,有关镀前处理溶液的配方及工艺条件见表7-3。
①化学除油。参考采用表7-3中方法1。
②冷水清洗。
③酸洗。酸洗浴,见表7-3中方法1或方法2。
④冷水清洗。
⑤活化。活化浴,见表7-3中方法3。
⑥冷水清洗。
⑦浸锌。浸锌浴,见表7-3中方法4。
⑧冷水清洗。
⑨闪镀铜。预镀铜浴,见表7-3中方法5。
⑩冷水清洗。
⑪去离子水洗或预热浸洗。
⑫预镀镍。预镀镍浴,见表7-3中方法6。
⑬冷水清洗。
⑭去离子水洗或预热浸洗。
⑮化学镀镍。按化学镀浴工艺参数操作。
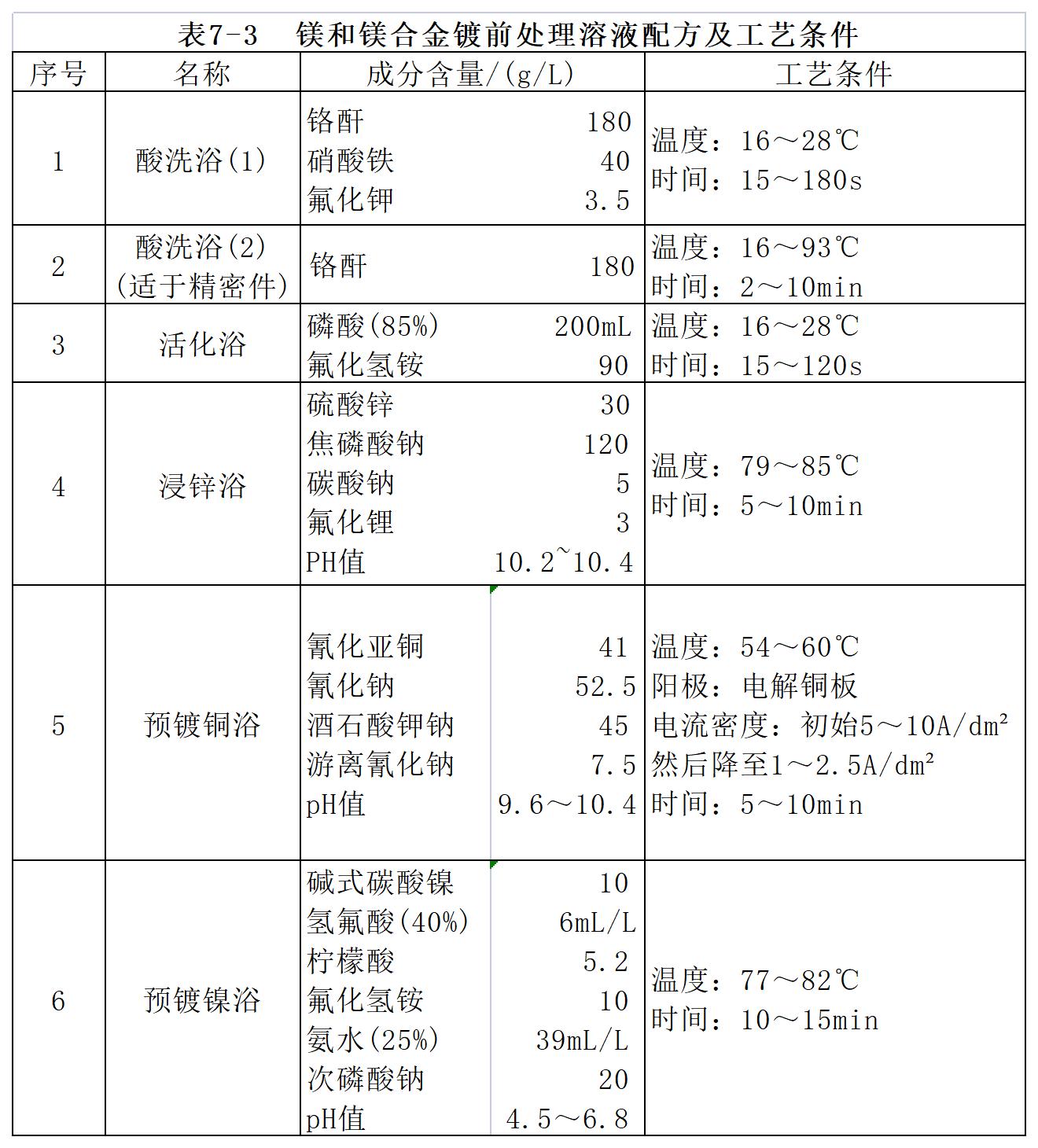
表7-3中列出的镁合金材料传统的酸洗工艺都是以铬酸或硝酸为基础的,适当改变酸洗液中各组分的含量,对于大部分的镁合金材料都能够起到较好的除锈效果。镁合金在含有Cl-和SO2-4的溶液中腐蚀速度较快,因此,多年来,人们都用铬酸对镁合金进行酸洗。但是,六价铬离子具有很强的毒性且易致癌,随着人们环保意识的增强,六价铬离子的使用正受到严格的限制。而酸洗液中的硝酸同样会产生"黄烟",即二氧化氮气体,对人身及环境造成损害。这就促使人们将目光转向不含铬酸及硝酸的“环保”型的酸洗溶液。
郭艳婷、李建三等人采用磷酸、硫酸等常规的酸取代铬酸,通过添加酸洗添加剂及缓蚀剂,研究出了不含六价铬的环保型镁合金酸洗液。研究结果表明,磷酸5mL/L,酸洗添加剂20mL/L,六次甲基四胺1.5g/L的酸洗工艺,可以取代铬酸,用作镁合金材料的酸洗液,摆脱长期以来镁合金酸洗液对铬酸的依赖,保护人体健康及自然环境。
表7-3中的预镀铜浴采用的是氰化物电镀工艺,不符合环保发展的趋势。因此,近年来有关镁合金化学镀镍前处理的研究工作都避免采用含氰化物的处理工艺,而是采用浸锌或二次浸锌后化学镀镍的工艺,也有学者对不浸锌直接化学镀镍的工艺进行了研究。比如,郭艳婷等人研究了浸锌+化学镀镍的前处理工艺,其工艺流程为:碱洗→水洗→酸洗→水洗→活化→水洗→预浸锌→化学镀镍。谷长栋等人对直接化学镀镍的工艺进行了研究,主要工序为:碱洗→酸洗→活化→直接化学镀镍。
7.钛及钛合金的镀前处理
金属钛的密度接近铝,钛合金具有优良的耐蚀性、热稳定性和高的比强度,在航空、航天工业中得到了较为广泛的应用,已成为先进航空发动机风扇、压气机盘、叶片等的主要结构材料。此外,钛合金还广泛应用于医疗、化工、石油和冶金等行业。
钛虽然耐蚀性很好,但其硬度不高,耐磨性差,导电性不良,而且不能钎焊。因此,在钛及钛合金件的表面通常必须进行镀覆处理,如采用化学镀镍来弥补这些不足。然而,钛合金表面有一层致密的自然氧化膜,即使经除油、浸蚀除去,经水洗接触空气后,瞬间又会重新生成氧化膜,在这层薄膜上难以沉积出结合力良好的镀层。因此在钛合金表面进行化学镀前必须首先解决好镀前预处理工艺问题。
典型的钛和钛合金的镀前预处理工艺如下,相关镀前预处理溶液的配方及工艺条件列于表7-4中。
①脱脂清洗。如碳钢镀前预处理工序步骤①~⑥。
②酸洗。酸洗浴,见表7-4中方法1。
③冷水清洗。
④浸蚀或电解浸蚀。浸蚀浴,见表7-4中方法2、方法3或方法4。
⑤冷水清洗。
⑥预镀镍活化。闪镀镍浴,见表7-1中方法5。
⑦冷水清洗。
⑧去离子水洗或预热浸洗。
⑨化学镀镍。按化学镀镍浴工艺参数操作。
⑩冷水清洗。
⑪干燥。
表7-4中传统的钛合金镀前预处理溶液含有六价铬,为了消除六价铬的污染,可以采取不含六价铬的镀前预处理工艺。工艺流程如下。
最新问答